F17 grade plywood is a specialized type of engineered wood that has gained significant attention in the construction industry, particularly for its application in heavy-duty formwork. Understanding its characteristics not only informs builders and contractors about its utility but also helps in making informed decisions regarding project materials. This article will explore the critical aspects of F17 grade plywood, emphasizing its importance in providing reliable, cost-effective solutions for heavy-duty construction projects.
Understanding the Basics of F17 Grade Plywood
F17 grade plywood is defined by its strength and durability, making it an ideal choice for applications requiring rigorous performance. The grading system for plywood is based on different factors including thickness, glue type, and strength. F17 is a high-grade specification that represents significant load-bearing capacity.
The Composition of F17 Grade Plywood
The composition of F17 grade plywood typically includes multiple layers of wood veneers, glued together with waterproof adhesive. These layers are arranged in a cross-banded manner, providing enhanced strength and stability. The wood used in creating F17 plywood can come from various species, commonly from high-density hardwoods, which contribute to its robustness.
This layered construction not only aids in reducing the effects of warping and splitting but also increases overall dimensional stability. Each layer is oriented in a direction that maximizes structural integrity, ensuring that it can support substantial loads without compromising on quality. Furthermore, the adhesives used in F17 plywood are often formulated to withstand extreme conditions, ensuring that the bond between layers remains intact even under stress.

Unique Characteristics of F17 Grade Plywood
One of the standout characteristics of F17 grade plywood is its high strength-to-weight ratio, which allows for ease of handling while maintaining impressive load-bearing capabilities. This property is essential in formwork settings where both stability and mobility are critical.
Additionally, F17 plywood is treated for water resistance, making it suitable for various weather conditions and environments. This aspect is particularly important for construction projects that may be exposed to moisture, as it reduces the risk of deterioration over time. The treatment process often involves the application of specialized coatings that enhance the plywood’s ability to repel water and resist fungal growth, further extending its lifespan and reliability in outdoor applications.
Moreover, F17 grade plywood is often used in high-stakes construction projects, such as bridges and high-rise buildings, where safety and performance are paramount. Its ability to endure heavy loads while maintaining structural integrity makes it a preferred material among engineers and architects. The versatility of F17 plywood also allows it to be utilized in various forms, including sheets, beams, and panels, catering to a wide range of construction needs and design specifications.
The Role of F17 Grade Plywood in Heavy-Duty Formwork
In heavy-duty formwork applications, where concrete molds are held in place, the reliability of materials used is paramount. F17 grade plywood plays a crucial role by providing both strength and stability to formwork systems.
The Strength and Durability of F17 Plywood
The strength of F17 grade plywood is specifically engineered to withstand high loads and pressures. This makes it an excellent choice for supporting wet concrete, which can be particularly heavy during the pouring process. Its durability ensures that the formwork can endure the stresses without risk of failure.
Moreover, the longevity associated with F17 plywood reduces the frequency of replacements in formwork, thereby minimizing downtime and overall project costs. These features collectively facilitate a smoother workflow on construction sites. Additionally, F17 plywood is often treated to resist moisture and decay, further enhancing its performance in challenging environmental conditions. This resistance is critical, as formwork is frequently exposed to wet concrete and varying weather, which can compromise lesser materials. Find more about environmental on https://www.plt.org/educator-tips/top-ten-benefits-environmental-education/
The Versatility of F17 Plywood in Construction
An additional advantage of F17 grade plywood is its versatility. It is not solely limited to formwork but can be used in various applications, including flooring, roofing, and structural components. This multi-functional attribute makes it a valuable asset in any construction project, allowing contractors to streamline their material usage.
Furthermore, owing to its lightweight design, F17 plywood can be easily transported and installed. This ease of use is especially beneficial in fast-paced construction environments where time and efficiency are of the essence. The plywood’s ability to be cut and shaped with standard tools also allows for customization on-site, enabling builders to adapt to unforeseen challenges without significant delays. Additionally, the aesthetic qualities of F17 plywood make it suitable for exposed applications, where its natural wood grain can enhance the visual appeal of a structure, combining functionality with design elegance.
Comparing F17 Grade Plywood with Other Plywood Grades
Understanding how F17 grade plywood compares to other plywood grades is essential for contractors deciding which materials best meet their project requirements. Each grade serves different functions based on its specifications and manufacturing standards.
F17 Plywood vs. Lower Grade Plywood
Lower grade plywood, such as F7 or F8, lacks the same level of strength and durability found in F17 plywood. While it may be more cost-effective upfront, the performance under load and resilience to environmental factors is not comparable. This can lead to increased maintenance costs and project delays due to material failure.
Moreover, lower grade options may not be suitable for heavy-duty applications, making F17 plywood a more prudent choice when the need for reliability is paramount. Projects that necessitate stringent safety standards and quality assurance will benefit tremendously from investing in higher-grade materials like F17.
Additionally, the manufacturing process for lower grade plywood often involves fewer quality checks and less stringent adherence to standards, which can result in inconsistencies within the sheets themselves. This variability can manifest as warping, delamination, or even structural weaknesses, which are particularly concerning in applications where safety is a top priority. Therefore, while the initial savings may be appealing, the long-term implications of using lower grade plywood can outweigh the upfront cost advantages. Learn more about adherence click here.
F17 Plywood vs. Higher Grade Plywood
In comparison to higher grade plywood, such as F22 plywood, F17 still holds its own in terms of performance while presenting a more cost-effective option. Higher grades offer greater strength for specific applications, but they may not always be necessary for every project.
For many construction scenarios, especially in standard heavy-duty formwork requirements, F17 provides ample strength and performance at a lower price point. This balance of quality and cost makes it a favored choice among builders.
Furthermore, F17 plywood is often manufactured with a focus on sustainability, utilizing responsibly sourced wood and environmentally friendly adhesives. This aspect not only appeals to eco-conscious builders but also aligns with the growing trend of sustainable construction practices. As regulations around environmental impact tighten, opting for F17 plywood can be a strategic choice that supports both project goals and corporate responsibility. The combination of reliability, cost-effectiveness, and sustainability makes F17 a compelling option in the competitive landscape of plywood grades.
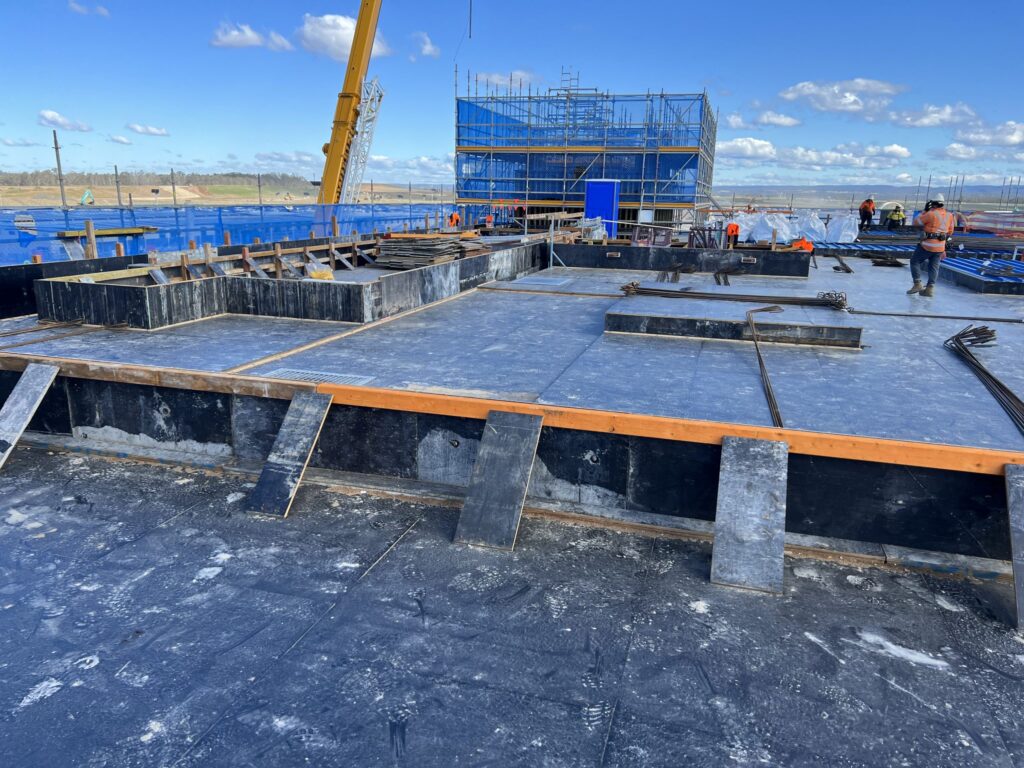
The Environmental Impact of Using F17 Grade Plywood
As awareness of environmental issues continues to grow, the sustainability of construction materials has become a vital discussion point. F17 grade plywood can be evaluated on various ecological parameters, making it essential for responsible contractors to consider its impact.
Sustainability of F17 Grade Plywood Production
Many manufacturers of F17 grade plywood are turning to sustainable practices in their production processes. This includes sourcing wood from managed forests and using eco-friendly adhesives in the manufacturing process. Such measures help decrease the overall carbon footprint associated with plywood production.
In recent years, certification schemes like the Forest Stewardship Council (FSC) have emerged, allowing consumers to make informed choices about the materials they are using. Choosing F17 plywood from certified sources guarantees that it has been produced in a manner that supports environmental conservation. Additionally, many manufacturers are investing in technology that enhances the efficiency of wood utilization, ensuring that less waste is generated during the cutting and processing phases. This not only conserves resources but also contributes to the overall sustainability of the industry.
Recycling and Disposal of F17 Grade Plywood
In terms of disposal, F17 grade plywood is not only durable but can also be recycled at the end of its lifecycle. This characteristic allows construction companies to adopt a more circular approach to materials, reducing waste and encouraging recycling practices.
If properly disposed of or recycled, F17 plywood can minimize the environmental impact commonly associated with construction waste. Using materials that support sustainable practices is increasingly becoming critical in the modern construction landscape. Moreover, the versatility of F17 plywood means it can be repurposed in various applications, from furniture making to decorative elements in interior design, further extending its lifecycle and reducing the demand for new materials. This adaptability not only promotes sustainability but also encourages innovative design solutions that align with eco-conscious building practices.
The Cost-Effectiveness of F17 Grade Plywood
The economic advantages of using F17 grade plywood are compelling, particularly when assessing factors like initial investment compared to long-term savings. Although the initial cost might be higher than lower grade plywood, the overall lifecycle cost can be significantly lower.
Initial Investment in F17 Grade Plywood
The upfront cost of F17 grade plywood is a worthy consideration for any construction budget. Builders often find that selecting higher-quality materials translates to better performance in the long run, reducing the frequency of repairs and replacements.
Additionally, when estimating project timelines, the use of durable materials like F17 can mitigate delays caused by material failure. Investing in reliable materials is often seen as a positive financial strategy for construction projects as it lays a strong foundation for successful outcomes. The structural integrity provided by F17 plywood also means that it can support heavier loads, making it an ideal choice for projects that require robust frameworks, such as commercial buildings and bridges. This added strength not only enhances safety but can also lead to lower insurance premiums, further contributing to the cost-effectiveness of the material.
Long-Term Savings with F17 Grade Plywood
Long-term savings associated with F17 grade plywood come from several interrelated factors. Reduced repair costs due to its durability, coupled with lower replacement frequency, equate to significant savings over time.
Moreover, fewer delays lead to enhanced productivity on job sites, which can result in faster project completion. This, combined with the material’s versatility, ensures that builders can use F17 plywood across various applications, ultimately capitalizing on its cost-effective attributes. The environmental impact of using F17 grade plywood also plays a role in its long-term savings. With its potential for being sourced from sustainably managed forests, it not only meets the growing demand for eco-friendly building materials but can also qualify projects for green building certifications. This can open doors to additional funding opportunities and incentives, making the initial investment even more justifiable. Furthermore, the energy efficiency of buildings constructed with high-quality materials like F17 plywood can lead to reduced heating and cooling costs, adding another layer of financial benefit over the lifespan of the structure.
In conclusion, F17 grade plywood is an essential choice for heavy-duty formwork, offering unique benefits in strength, versatility, and environmental responsibility. By detailing its characteristics and advantages, we can appreciate its role in modern construction projects and its importance in promoting a sustainable and efficient building environment.
Read about f14 grade plywood at: F14 Grade Plywood