In the realm of construction, innovation plays a vital role in advancing the industry and improving building techniques. One area that has seen significant development is formwork, with the emergence of Laminated Veneer Lumber (LVL) formwork. This technology has quickly gained popularity among builders, revolutionizing the way structures are constructed. Let’s delve into the reasons why LVL formwork is a game-changer for builders.
Understanding LVL Formwork
Before we explore the advantages of LVL timber buy, it’s crucial to grasp the fundamentals of this construction technique.
LVL formwork, short for Laminated Veneer Lumber formwork, is a popular choice in the construction industry due to its strength, durability, and versatility. The process of creating LVL involves bonding together multiple layers of thin wood veneers with high-quality adhesive under heat and pressure. This results in a material that exhibits consistent strength and dimensional stability, making it ideal for supporting heavy loads during concrete construction projects.
The Basics of LVL Formwork
LVL formwork involves using engineered panels made from multiple layers of thin wood veneers. These veneers are bonded together using top-grade adhesive, creating a robust and dimensionally stable material. The resulting LVL panels serve as the primary support system for creating temporary molds, commonly known as formwork, that shape the poured concrete into desired structures.
One of the key advantages of LVL formwork is its ability to be easily customized to fit various shapes and sizes, allowing for the construction of complex architectural designs with precision and efficiency. Additionally, LVL formwork is known for its reusability, making it a cost-effective and sustainable option for construction projects.
Key Components of LVL Formwork
A successful LVL formwork system relies on several crucial components. These include adjustable props, beams, walers, and panel connectors. Combined, these elements provide a reliable framework for pouring and curing concrete, ensuring optimal structural integrity.
Adjustable props are used to support the formwork and transfer the loads to the ground, while beams and walers help distribute the weight of the concrete evenly across the formwork system. Panel connectors play a vital role in securely joining the LVL panels together, creating a seamless surface for the concrete to be poured onto.
The Advantages of LVL Formwork for Builders
Now that we understand the basics, let’s explore the unparalleled benefits of LVL formwork in the construction industry:
Improved Durability and Strength
The use of LVL panels in formwork significantly enhances the durability and strength of the entire structure. The superior load-bearing capacity of LVL ensures that the formwork can withstand the pressure exerted by the wet concrete, preventing deformation and collapse. This feature is particularly crucial in high-rise construction projects.
Moreover, LVL formwork offers excellent dimensional stability, meaning it is less susceptible to warping or twisting compared to traditional timber formwork. This stability ensures that the concrete structure maintains its intended shape and alignment throughout the curing process, resulting in a more precise and uniform final product.
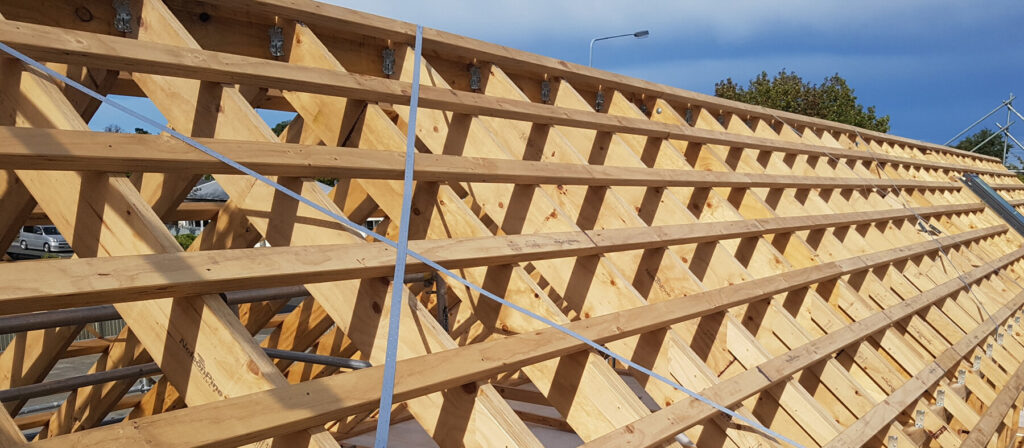
Enhanced Efficiency and Productivity
LVL formwork enables builders to achieve higher levels of efficiency and productivity. The prefabricated nature of LVL panels reduces the time required for formwork assembly, allowing for faster construction cycles. With LVL formwork, builders can expedite the building process without compromising quality.
Furthermore, the smooth and even surface of LVL panels facilitates easy demolding, reducing the time and effort needed for formwork removal. This streamlined process not only accelerates construction timelines but also enhances overall project efficiency by enabling quicker reusability of formwork components.
Cost-Effective Building Solution
One of the most appealing aspects of LVL formwork for builders is its cost-effectiveness. LVL panels can be reused several times, minimizing material wastage and reducing overall construction costs. Additionally, the speed of construction with LVL formwork translates to lower labor costs and improved project economics.
Moreover, the long-term durability of LVL formwork contributes to cost savings by reducing the need for frequent replacements or repairs. This extended lifespan, coupled with the material’s resistance to moisture and chemicals, ensures that builders benefit from a sustainable and economical formwork solution in the long run.
The Role of LVL Formwork in Modern Construction
LVL formwork has gained significant traction in both residential and commercial construction projects due to its versatility and adaptability.
Engineered wood products like Laminated Veneer Lumber (LVL) have revolutionized the construction industry by offering a sustainable and cost-effective alternative to traditional formwork materials. LVL is made by bonding multiple layers of wood veneers together, creating a strong and durable material that can withstand the pressures of concrete placement.
LVL Formwork in Residential Construction
In residential construction, LVL formwork proves invaluable for creating complex concrete structures such as walls, slabs, and staircases. The ability to customize LVL panels to fit various architectural designs ensures efficient and precise construction.
Moreover, LVL formwork’s smooth surface finish reduces the need for extensive finishing work, saving both time and labor costs during the construction process. Its lightweight nature also makes it easier to handle on-site, improving overall efficiency and safety for workers.
LVL Formwork in Commercial Construction
The utilization of LVL formwork is equally prominent in commercial construction projects. From skyscrapers to shopping centers, LVL formwork enables builders to construct large-scale structures with precision and speed.
Additionally, LVL formwork’s dimensional stability and high load-bearing capacity make it an ideal choice for commercial projects where structural integrity is paramount. The versatility of LVL panels allows for the creation of intricate architectural features and unique designs, giving commercial buildings a modern and aesthetically pleasing appearance.
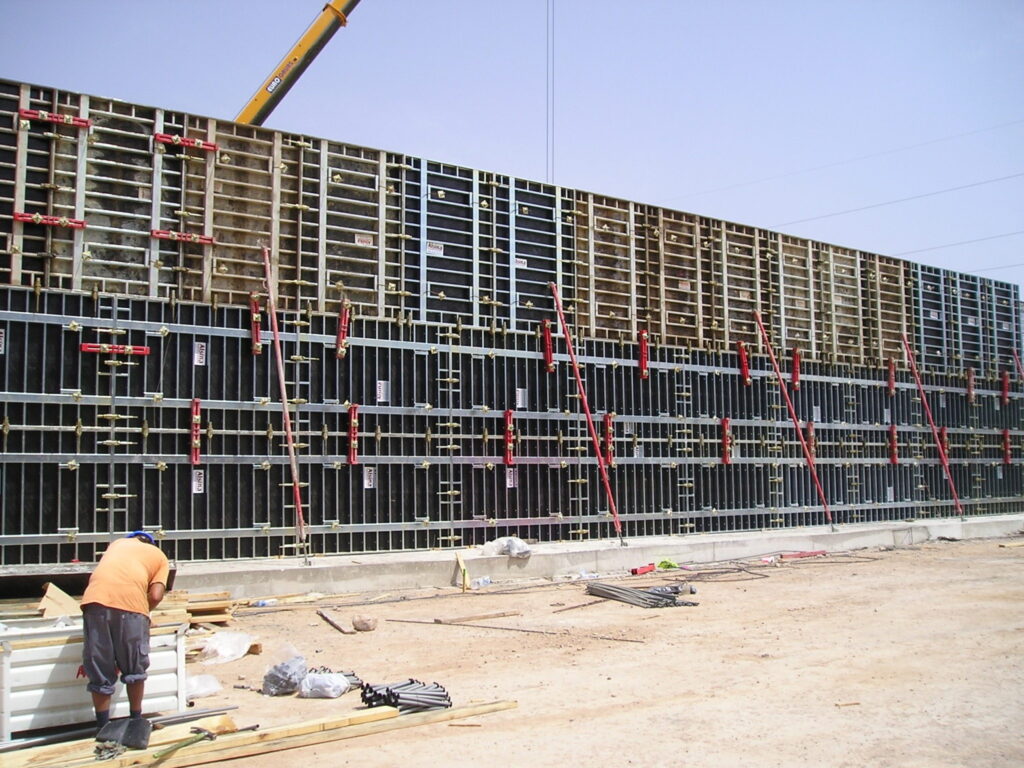
Safety Aspects of LVL Formwork
Safety is a paramount concern in the construction industry, and LVL formwork prioritizes worker well-being without compromising productivity.
When it comes to construction projects, ensuring the safety of workers is not just a legal requirement but also a moral obligation. LVL formwork goes above and beyond to provide a secure working environment that instills confidence in the construction team.
Safety Features of LVL Formwork
LVL formwork incorporates several safety features to protect workers during construction. Anti-slip surfaces, handrails, and guardrails ensure stability and prevent accidents. Builders can have peace of mind, knowing that LVL formwork promotes a secure working environment.
Moreover, the modular design of LVL formwork allows for easy installation and dismantling, reducing the risk of accidents during these processes. The precision engineering of these components ensures a snug fit, eliminating any potential hazards that may arise from loose or unstable formwork.
Ensuring Worker Safety with LVL Formwork
By minimizing the need for manual handling and reducing labor-intensive tasks, LVL formwork reduces the risk of work-related injuries. This technology allows builders to prioritize worker safety, resulting in a positive impact on the overall project timeline and worker satisfaction.
Additionally, the lightweight nature of LVL formwork makes it easier to maneuver on-site, further decreasing the likelihood of strains and sprains among workers. This emphasis on ergonomics not only safeguards the well-being of the construction team but also enhances efficiency and productivity on the job.
The Future of Construction: LVL Formwork
With its outstanding performance and undeniable benefits, LVL formwork is set to shape the future of construction.
LVL formwork, short for Laminated Veneer Lumber formwork, represents a revolutionary approach to construction. Its innovative design and structural integrity make it a preferred choice for builders and developers looking to streamline their processes and increase efficiency. By utilizing LVL formwork, construction projects can achieve higher precision and faster completion times, ultimately leading to cost savings and improved project outcomes.
Sustainability and LVL Formwork
Environmental considerations are becoming increasingly critical in construction. LVL formwork aligns with sustainable practices by utilizing timber, a renewable resource, as its primary material. As the industry continues to emphasize eco-friendly solutions, LVL formwork will play a crucial role in meeting sustainability goals.
Furthermore, the manufacturing process of LVL formwork involves minimal waste generation, contributing to a more environmentally friendly construction approach. This focus on sustainability not only benefits the environment but also enhances the overall reputation of construction projects utilizing LVL formwork.
Technological Advancements in LVL Formwork
The evolution of LVL formwork is ongoing, with ongoing research and technological advancements. These improvements aim to enhance the performance, durability, and ease of use of LVL formwork, further cementing its position as a game-changer in the construction industry.
Recent technological advancements in LVL formwork include the integration of smart sensors and monitoring systems to provide real-time data on structural integrity and load-bearing capacity. These innovations not only improve safety on construction sites but also allow for more precise decision-making during the building process. As technology continues to advance, LVL formwork is poised to become even more efficient and versatile, setting new standards for construction practices worldwide.
Conclusion
In summary, LVL formwork revolutionizes the way builders construct structures, offering a host of advantages in terms of durability, efficiency, cost-effectiveness, and safety. Its versatility and adaptability make it a go-to choice for both residential and commercial projects. Looking ahead, LVL formwork will continue to shape the future of construction, providing sustainable and technologically advanced solutions for builders worldwide.
More to read: Advanced SEO Tools that an Agency May Not Show You